Undercover999
Rough_Rock
- Joined
- Nov 15, 2011
- Messages
- 62
I'm trying to be a little different and am making an engagement ring for my intended... at home. I have no experience with this, but I'm pretty handy, and if it doesn't work I'll just scrap it and buy one.
She has told me, repeatedly, that she wants a THIN band. She would definitely not like anything that looks heavy, her #1 concern is that it be THIN. I don't really know what that means in jewelry terms, but I'm finding 2mm to be roughly the thinnest commonly available so thats my starting point.
First question:
Will 2mm wide x 1.5mm "tall" band be adequate in terms of durability, etc? And 2mm won't be TOO thin looking, will it? I wouldn't want her to think I tried to skimp on the metal, haha. I'm going to use some "heirloom" gold that was given to me when I was born so the material will be 14k palladium white gold. Here is the design I came up with, borrowing features from rings she said she liked and mashing them together:
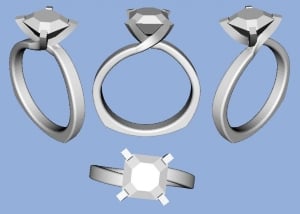
I machined a wax block so I could make some rubber molds and make a urethane (plastic) test run.
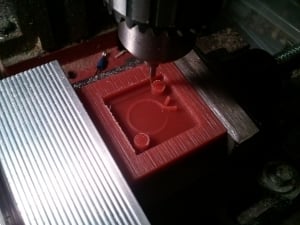
Here's my test run with my diamond popped into it.
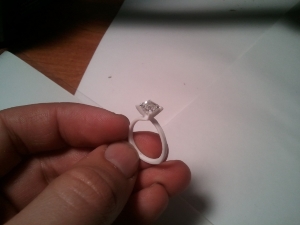
Band width looks OK to you folks? I've asked her friends and they're all like "omg sparkles?!?!" and haven't given me any real feedback. My taste in rings would be somewhat opposite, I'd want something HEAVY so it feels expensive and you could use it for bashing your enemies... but she wouldn't agree. I have no idea.
Second question:
I have been annoying all my friends by asking them to see their rings and measuring them with calipers so I have a certain starting point already, but what is a good size for the prongs? I believe I'm at roughly 1mm square now, and again they'll be 14k palladium white gold holding a 1.53 Asscher. Will that be good enough/fairly robust?
Thanks!
She has told me, repeatedly, that she wants a THIN band. She would definitely not like anything that looks heavy, her #1 concern is that it be THIN. I don't really know what that means in jewelry terms, but I'm finding 2mm to be roughly the thinnest commonly available so thats my starting point.
First question:
Will 2mm wide x 1.5mm "tall" band be adequate in terms of durability, etc? And 2mm won't be TOO thin looking, will it? I wouldn't want her to think I tried to skimp on the metal, haha. I'm going to use some "heirloom" gold that was given to me when I was born so the material will be 14k palladium white gold. Here is the design I came up with, borrowing features from rings she said she liked and mashing them together:
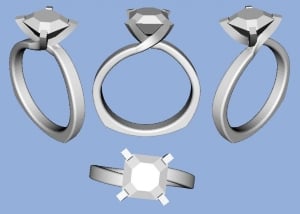
I machined a wax block so I could make some rubber molds and make a urethane (plastic) test run.
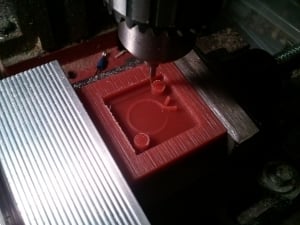
Here's my test run with my diamond popped into it.
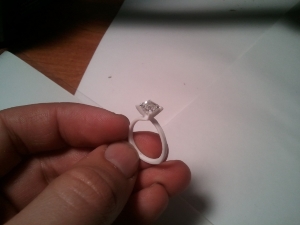
Band width looks OK to you folks? I've asked her friends and they're all like "omg sparkles?!?!" and haven't given me any real feedback. My taste in rings would be somewhat opposite, I'd want something HEAVY so it feels expensive and you could use it for bashing your enemies... but she wouldn't agree. I have no idea.
Second question:
I have been annoying all my friends by asking them to see their rings and measuring them with calipers so I have a certain starting point already, but what is a good size for the prongs? I believe I'm at roughly 1mm square now, and again they'll be 14k palladium white gold holding a 1.53 Asscher. Will that be good enough/fairly robust?
Thanks!