- Joined
- Sep 28, 2017
- Messages
- 303
Looking into setting a loose diamond and have been getting some quotes from a few different vendors. I noticed something while looking at some of their past work and was hoping you all could help me figure it out! All images are from reputable, well reviewed vendors and I think all of the settings are beautiful but it seems like some settings appear more lightweight to me (top two images). They almost look tinny. None of these are hand-forged as far as I know and I am familiar with the density of hand forged items and the work that goes into that but I'm wondering why the appearance of cast settings varies so widely. Anyone with expertise or ideas let me know!
Thank you!
VERSUS
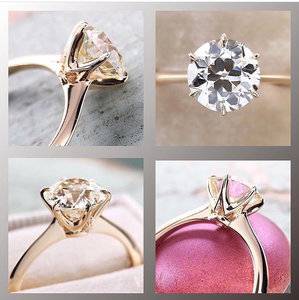
Thank you!
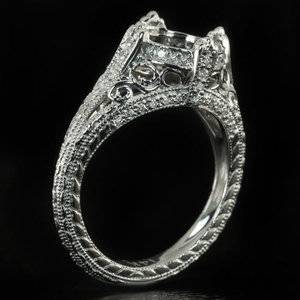
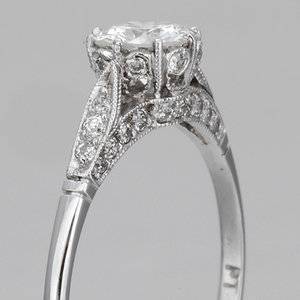
VERSUS
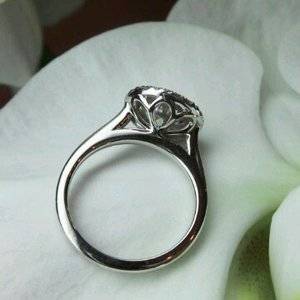
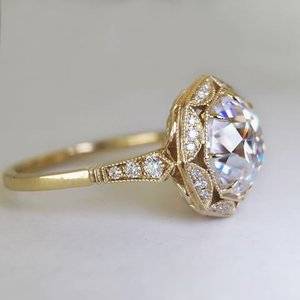
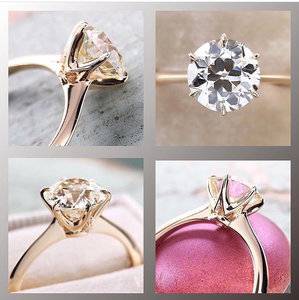