speedy0514
Rough_Rock
- Joined
- Jun 8, 2011
- Messages
- 25
Hi everyone -
I've come across an unexpected issue with my newly purchased e-ring. For background, I bought my center stone online from BGD and took it to my local jeweler in Chicago to have it set in a custom 18k gold ring (alloyed with palladium) that was designed and cast out in New York. When I went to pick up the ring the day before my planned proposal, I inspected the ring and found a small round defect on the underside of the band. It almost looks like a small hole, I assume caused by an air pocket in casting. See the picture below...
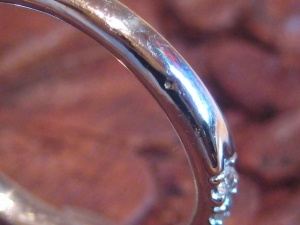
So I talked with my jeweler and agreed that I would pay the balance on the ring so I could go ahead with the proposal with the understanding that we would be able to get it fixed at a later date or completely re-cast so I could just bring the defective ring back to have the diamond re-set on site. I just wanted to make sure that my fiance would not have to be without her ring for more than a few hours during the process.
So now I have to decide what to do among a few options. I received this statement from the designer in New York when my local jeweler sent him the photo above:
"This is the easiest type of porosity, it’s an isolated air bubble. It probably will take 10 minutes to fix." Unfortunately, my local jeweler will not fix this in-house, and they will need to ship it back to New York for repair. I definitely don't want to do this because I know my fiance would not want to be without her ring for several days.
I have also been told that I could also go ahead and have the ring re-cast, as we agreed upon at the time of purchase.
So here are my questions:
1. Is this a common type of defect in workmanship, and does it normally make it through inspection? It is fairly obvious to the unaided eye, so it surprises me that no one noticed before I was presented with the ring.
2. Is there reason for me to be concerned about other possible defects in workmanship that may not be noticeable on the exterior of the band?
3. While re-casting the ring would be the least trouble for me, is it worth the risk considering I'm really pleased with everything about my defective ring aside from the small imperfection? I fear that I could get a replacement with even more issues than the first.
4. Is this the type of defect that a jeweler in Chicago should be able to fix with ease? What type of cost would go along with this type of fix?
5. And lastly, what would you choose to do? I'm really having trouble deciding how to proceed.
Thank you all in advance for your input.
I've come across an unexpected issue with my newly purchased e-ring. For background, I bought my center stone online from BGD and took it to my local jeweler in Chicago to have it set in a custom 18k gold ring (alloyed with palladium) that was designed and cast out in New York. When I went to pick up the ring the day before my planned proposal, I inspected the ring and found a small round defect on the underside of the band. It almost looks like a small hole, I assume caused by an air pocket in casting. See the picture below...
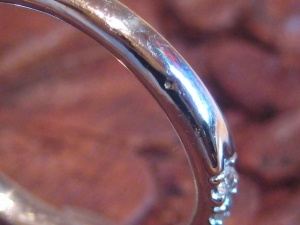
So I talked with my jeweler and agreed that I would pay the balance on the ring so I could go ahead with the proposal with the understanding that we would be able to get it fixed at a later date or completely re-cast so I could just bring the defective ring back to have the diamond re-set on site. I just wanted to make sure that my fiance would not have to be without her ring for more than a few hours during the process.
So now I have to decide what to do among a few options. I received this statement from the designer in New York when my local jeweler sent him the photo above:
"This is the easiest type of porosity, it’s an isolated air bubble. It probably will take 10 minutes to fix." Unfortunately, my local jeweler will not fix this in-house, and they will need to ship it back to New York for repair. I definitely don't want to do this because I know my fiance would not want to be without her ring for several days.
I have also been told that I could also go ahead and have the ring re-cast, as we agreed upon at the time of purchase.
So here are my questions:
1. Is this a common type of defect in workmanship, and does it normally make it through inspection? It is fairly obvious to the unaided eye, so it surprises me that no one noticed before I was presented with the ring.
2. Is there reason for me to be concerned about other possible defects in workmanship that may not be noticeable on the exterior of the band?
3. While re-casting the ring would be the least trouble for me, is it worth the risk considering I'm really pleased with everything about my defective ring aside from the small imperfection? I fear that I could get a replacement with even more issues than the first.
4. Is this the type of defect that a jeweler in Chicago should be able to fix with ease? What type of cost would go along with this type of fix?
5. And lastly, what would you choose to do? I'm really having trouble deciding how to proceed.
Thank you all in advance for your input.