- Joined
- Dec 6, 2014
- Messages
- 2,118
Just thought I'd drop in with this pic, we have begun working on cabs at home now with the new machine. We've started by using the freebies we got with the machine to 'break in' the wheels. When you first get the wheels for a cabbing machine you will find they can be a bit rough for their specified grit so the best thing to do is to cut some cheaper stuff to take away that rough outside layer and smoothen the wheel a bit more. This is proving to be vital with the 1200 grit diamond wheel I have as it should be polishing but it's cutting away more material than I want (I am considering getting a 1200 nova style wheel, any pros think that may be the way to go?). I also did dremel polishing today and the results have been quite pleasing! I just have to figure out a few little things for my polishing setup and develop my technique some more.
I'm hoping to get that little white opal finished as soon as I'm happy to use opal on the machine so hopefully it won't be too long until that's been fixed and finished!
Mrs Jordy has been doing silver wire wrapped pendants with the cabochons we've been making, if anyone is interested then I will post pics of those as well!
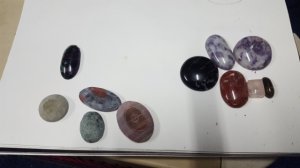
I'm hoping to get that little white opal finished as soon as I'm happy to use opal on the machine so hopefully it won't be too long until that's been fixed and finished!
Mrs Jordy has been doing silver wire wrapped pendants with the cabochons we've been making, if anyone is interested then I will post pics of those as well!
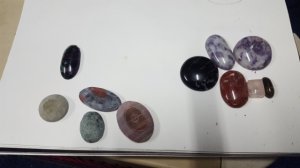